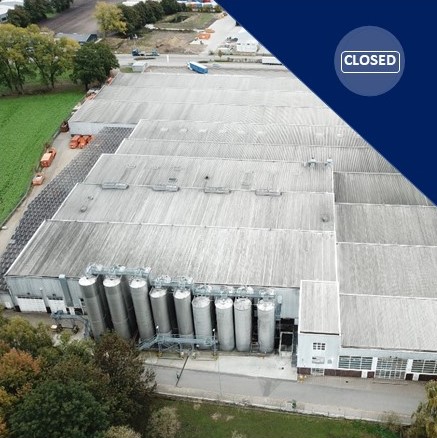
Business closures and plant closings: what to do with surplus equipment?
Closing a location is a difficult decision and many decision-makers are faced with new areas of responsibility. How do I dismantle my production facilities safely and professionally? Do the systems have to be professionally cleaned before dismantling? Who takes care of the surplus machinery and what is their value? There are several options that can be considered in this context.
Internal relocation of machinery
In large corporations and medium-sized companies with several locations, an internal relocation of the surplus machinery is usually the preferred choice. Special high-quality machines with the corresponding residual book values can thus be reused in the organization in a way that conserves resources. However, relocating all process plants and machinery is often not worthwhile, as the dismantling costs, transport, and storage costs for various simpler process machines (for example storage tanks, stirred vessels or outdated old machinery) exceed their replacement value.
Industrial auction houses
Another option for the disposal of used production machinery from plant closures are specialized industrial action houses. These usually bring a broad network of prospective buyers with them, many of them also outside of Europe. This option is therefore primarily suitable for process systems and machinery which are of relevance and interest for an international client spectrum and less for interested parties on a regional or national level. Examples might be older dairy machines or process machinery with an outdated technical focus.
A clear disadvantage of industrial actions is the often very complex handling procedure. It is common for certain bidders to withdraw from their purchase after the auction has ended because of misunderstandings, payment problems or time bottlenecks. The coordination of the dismantling and loading of the lots can also become very complex if a large number of trucks arrive in a few days to pick up individual orders. Even after an auction, customers to try to approach the seller with technical queries. In addition, an auction is often associated with a lot of publicity, which can have negative effects in the context of a business closure. From a holistic point of view, this disposal option is the most time-consuming, and it often ties up staff resources for months to support the small-scale coordination of the large number of individual buyers.
Used machinery & equipment dealers
Selling machinery to a used equipment dealer is often the most discrete and efficient way to keep the complexity of a production dismantlement as low as possible. Leading trading companies for used tanks & machinery have their own or trusted dismantling partners who are trained in the decommissioning and dismantling of complex production facilities. This ensures that clients can expect a holistic offer for both the purchase of used machinery as well as the corresponding dismantling services in one go. After the deal is signed, payment is typically made in advance, for a maximum in transparency and transaction safety.
Behälter KG has been active in purchasing & dismantling used tanks, reactors and used equipment for over 50 years. Our references range from the explosion-proof clean room of a pharmaceutical company, through larger process plants within the dairy industry up to multi-story production facilities in the specialty chemicals industry.
Due to our long-standing partnerships, we not only take care of used stainless steel tanks & related machines, but also deal with complex process machines, pharmaceutical equipment, and other industrial goods.